Posted: May 23, 2022
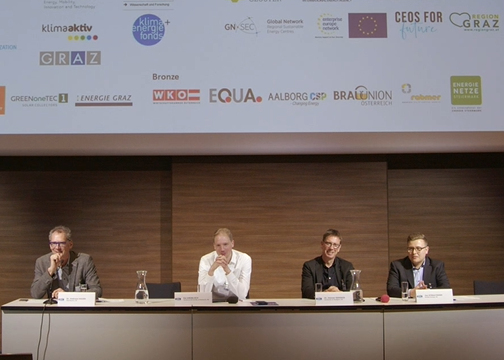
Source: AEE INTEC (Photo taken from the recording of the session)
The session Emerging Heat and Cold Storages during the ISEC conference in April in Austria was a deep dive into thermochemical heat storage. Two speakers from the German research project Heat2Share presented technical improvements at the material, component and system levels of a thermochemical storage unit used in district heating. The session was moderated by Dr Andreas Hauer, who co-chairs the IEA SHC Task 67 Material and Component Development for Thermal Energy Storage together with Dr Wim van Helden (AEE INTEC). Hauer works at the Bavarian Centre for Applied Energy Research – ZAE Bayern.
https://solarthermalworld.org/news/develop-stable-and-reliable-compact-thermal-energy-storages/
“In Task 67 we aim at gaining experience in designing optimised heat exchangers and reactors for thermochemical storage. The research project Heat2Share is progressing well towards delivering such insights,” explained Hauer. It aims at building a modular thermochemical storage system based on improved components and testing it in a real environment. The project group
profited from a previous three-year development phase by the German material research company Zeosys Energy and wants to raise the technology readiness level of this storage concept from four to seven by improvements at the material, component and system levels.
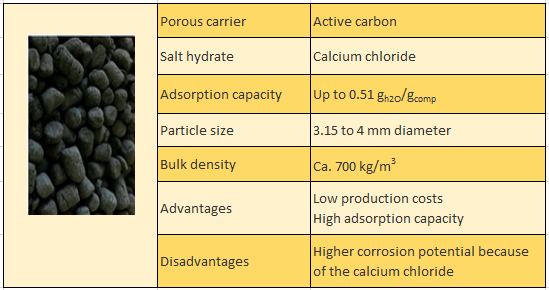
Specification of the new composite material for thermochemical storage tanks
Source: Heat2Share
Sorption material for low temperatures
Zeosys Energy tested a thermochemical material for low temperatures (40 to 100 °C) based on a new composite sorption material, which is an alternative to the zeolites that have been used in prototypes as a sorption material for high-temperature applications (100 to 300 °C). The composite consists of active carbon as a porous carrier impregnated with calcium chloride. “We were able to prove that composites are suitable for low-temperature heat between 40 to 100 °C for longer periods without vacuum leakages”, said Jan Straatmann of Zeosys Energy during his presentation.
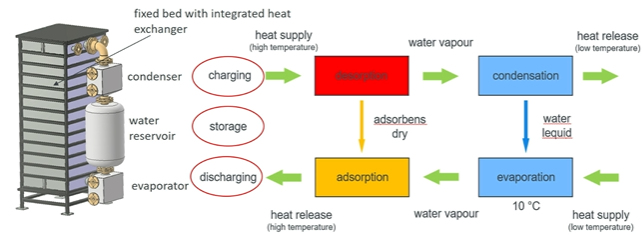
Figure 1: Functionality of a closed adsorption storage system
Source: Heat2Share
Closed adsorption storage system
Dr Henner Kerskes of the University of Stuttgart, Germany, explained in his presentation how the adsorption storage system of Heat2Share works. The system consists of a closed, evacuated vessel that includes a heat exchanger and is filled with particles of the composite. Furthermore, an external water reservoir is needed, which is connected at the upper end to a condenser and at the lower end to an evaporator (see figure 1).
During the charging phase the sorption material is dried. This means that a high-temperature heat source flowing through the internal heat exchanger drives out the water molecules that are bound to the sorption material. The emerging water vapour is then condensed in the condenser and the water is stored in the reservoir. “If we prevent the sorption material in the vessel from containing any moisture, then we can store the heat without losses as long as we want,” said Kerskes and added: “For discharging we have to bring the water vapour and sorption material together again.” A low-temperature heat source is used to evaporate the water and this is typically done at around 10 °C and 10 mbar. Then the water vapour flows into the sorption material in the vessel. During the adsorption of the water vapour heat is released and this heat can be extracted by the heat exchanger, for example for heating purposes.
“We have operated a vacuum-sealed thermochemical storage system for three years and have detected no malfunctions and no significant vacuum losses during this long period,” said Straatmann, summarising the experiences prior to Heat2Share.
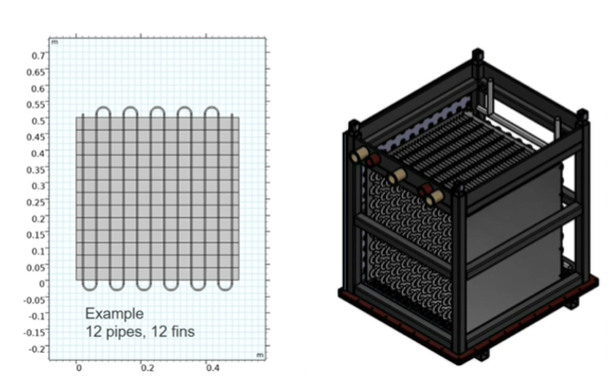
Figure 2: 2D and 3D model of the fin-shaped heat exchanger used in the Heat2Share thermochemical demonstration units.
Chart: Heat2Share
Corrosion-resistant heat exchanger
Completely different requirements are placed on heat exchangers in sorption materials than in water storage tanks. In thermochemical storage tanks, fin-shaped heat exchangers are predominantly used (Figure 2). Improving their performance both in terms of material and geometry is one of the major objectives of Task 67. Straatmann explained the novelties related to the heat exchanger tested in Heat2Share: “We use a copper-nickel alloy that allows a good heat transfer but also an increased corrosion resistance. We have also minimised the fin spacing to ensure that every particle has contact to the heat exchanger surface.” Simulations by Kerskes's research group at the University of Stuttgart suggested that a small gap between the fins results in higher power output of the storage units. Kerskes saw the optimised distance between the fins at around 10 mm for this material and this purpose.
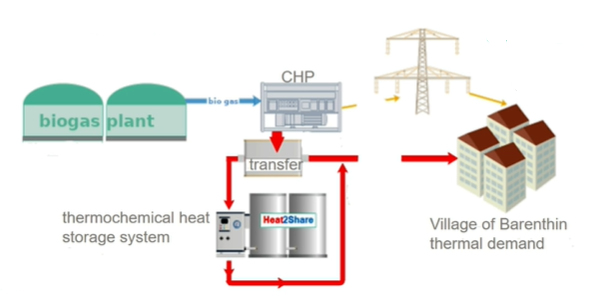
Figure 3: District heating system at Barenthin, a village north of Berlin, Germany
Source: Heat2Share
Intensive testing in a district heating system
The project partners of Heat2Share are now about to build a scalable modular storage system using innovative materials and components. The storage system consists of four units with 250 kg sorption material each, which will be interconnected and then integrated into a district heating system to be intensively tested.
The heating centre is a biogas-driven combined heat and power plant that provides heat to 29 residential buildings (see figure 3). The thermochemical storage will be connected between the feed line at around 75 °C and the return line at around 55 °C as short-term storage. Kerskes emphasised that these are slightly unfavourable conditions because of the small temperature difference between charging and discharging, but nevertheless this integration gives the project partners the possibility to test the prototypes under real conditions.
Organisations mentioned in this news article: